Getting the Scratches Out: Suggestions for Clear Parts and Canopies
by John Miller
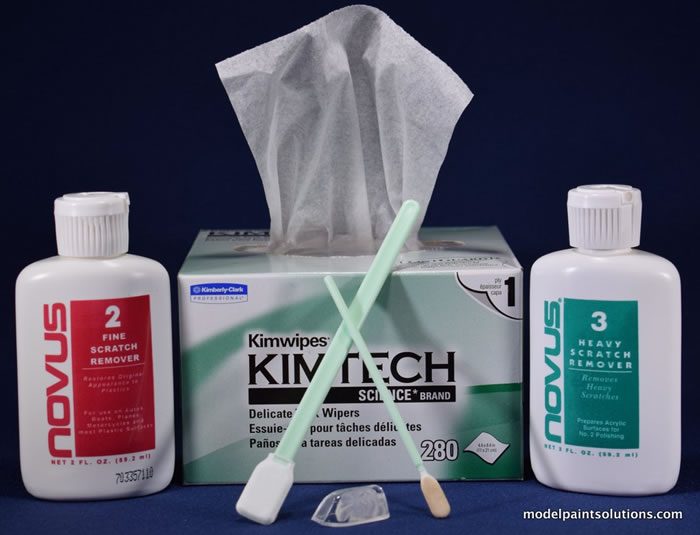
|
Getting the Scratches Out |

Hobby Boss' 1/72 Macchi C.200 Saetta is available online from Squadron for only $10.99!
Let me say up front that I have a canopy fetish. There, I said it: the truth is out and I feel so much better. I suspect that if you’re a scale modeler, you may have a similar preoccupation with parts made of clear styrene.
If that’s the case you’ll probably agree that the focal point of the average aircraft build is the canopy/cockpit. There's a lot going on in there and the eyes just seem to be drawn to it. That being the case, extra effort to ensure the canopy is as clear as possible will be time well spent.
We'll start with some suggestions for removing clear parts from their sprue then move on to polishing out scratches thence dipping in a clear coat. Lastly, we’ll consider ways of gluing the polished part onto the model. We’ll also take a quick look at some techniques used to sand and polish clear parts after being glued in place.
As with any "How-To" article what follows is a description of techniques developed from years of trial and error at my workbench. That said, their are as many ways to remove scratches from clear parts as there are modelers developing sore shoulders from hours of wet sanding and polishing. With that in mind please take whatever you find useful from the following suggestions, combine it with your own experience and develop a technique that best suits you. I hope you find something useful.
Removing Clear Parts from the Sprue |
A lot of damage can occur while removing a clear part from it's sprue especially if the sprue gate is large and connects to a slender or thin portion of the part like a canopy frame. If mishandled, removal of a clear part can result in a crack or crazing of the plastic from stress. The chance of this happening increase if the part is removed with an X-Acto blade or a sprue cutter.
I prefer to separate the clear part from it's sprue using a micro saw. These are available online from multiple sources.
To remove a canopy piece with a micro saw I line the saw blade up with the gate so it’s flush with the canopy piece. As with any saw, I try to not exert a downward pressure on the saw while using it. Instead, try to move the saw back and forth carefully while maintaining proper alignment. The accompanying photo shows a cut that’s been made about ½-way through the sprue gate of a 1/72 Me-109 canopy.
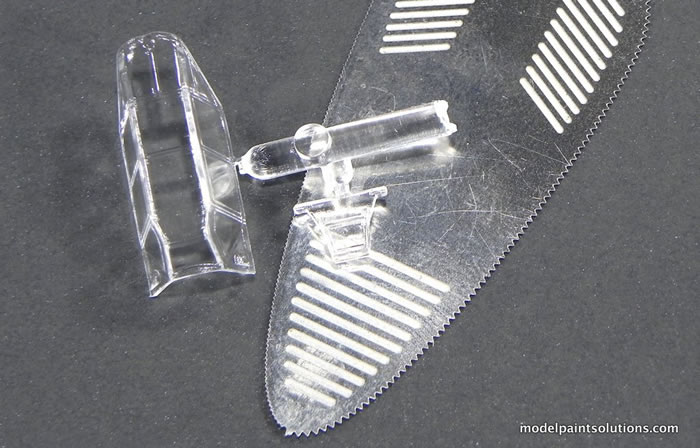
Once removed from the sprue, any portion of the stub remaining is easily removed using a folded piece of Alpha Abrasives 1,000 grit sandpaper. To ensure the clear (window) portions of the part are not damaged during sanding, they're first covered with a piece of Tamiya tape. I then carefully wet sand the remaining stub under magnification (3x lenses) using cold, soapy water. Alpha 1,000 sandpaper is awesome stuff to use on clear parts, as it doesn't cause as many unwanted scratches, as does conventional sandpaper because the surface is finer.
Once the canopy is removed from the sprue and the attach point smoothed over with 1,000 grit paper, I set about buffing the canopy in preparation for a quick dip in Future.
Buffing and Polishing Clear Parts and Canopies |
The procedures described below rely on a step-wise transition from the most to least abrasive tool when removing scratches. Where on the spectrum you should start depends on both the severity of the scratches and the hardness of the plastic you're polishing. With practice and experience you'll get the feel of where on this spectrum you should begin.
Clear Parts with No Scratches:
Even if the clear part has no scratches or blemishes I'll give it a light buffing with a dry Kimwipe tissue. I do this because Kimwipes are optical grade delicate task tissues that are specially treated so as to dissipate static electricity. This is important. If the clear part being prepped has been sanded it's quite likely to have a static charge. This residual charge will attract small particles of dust, putty etc that will stick to the clear part----usually after it's been glued in place :( If you're an aircraft or car modeler, I'll bet you've been treated to the site of dust and shcmutz sticking to the inside of your recently glued windshield or canopy at least once: maybe more? A quick buffing with a Kimwipe will go a long way to prevent this from happening.
Small Shallow Scratches:
Very fine, shallow scratches can be buffed out with Novus Plastic Polish #2. Depending on the size of the part, I apply the polish with a small or large Microfiber swab and buff the plastic using a light circular motion. The small microfiber swab works great if the scratches are on the inside of the part. I will periodically wipe the polish from the part to determine if the scratches are being buffed out. If the scratches are not disappearing, as they should, I'll switch to a Polyester swab, which gives a bit more "bite" than do the swabs made of microfiber. When I'm satisfied with the results, the part receives a final buffing with a Kimwipe.
Moderately Deep Scratches:
For scratches too deep to be buffed out with Novus #2, I use Novus Plastic Polish #3 applied and buffed with a polyester swab. The part is periodically wiped clean with a Kimwipe to assess how well the technique is working. Once the deepest scratches have been removed, I'll switch to Novus #2 applied and buffed with a microfiber swab. I'll continue with this combination until the part is practically clear and then do a final buffing with a Kimwipe.
Deep Scratches:
If the offending scratches are too deep to be removed with Novus #3, I'll start the buffing process with Alpha 600 or 1,000 grit abrasive used with cold soapy water. Once the scratches are removed, I'll switch to Alpha 40,000 or 60,000 grit sanding films or the grey portion of the Flex-Pad Triple-grit polisher followed by wet buffing with micromesh 3200 or 3600 pads. When the parts starts to look translucent, I'll switch to Novus 3# applied and buffed with a polyester swab followed by Novus #2 buffed with a microfiber swab. As always I finish the process with a final buffing with a Kimwipe.
Scratches so Deep it Hurts to Look at Them :(
I'm guessing we've all faced a situation like this whether of our own making or the result of a clear part banging around inside the box. To remove scratches this deep I'll start with Alpha Abrasives 400 or 600 grit paper used with cold soapy water. It's best to use the lowest grit possible that removes the scratches while doing as little damage to the remainder of the part. When using these abrasives on clear parts I buff using a light circular motion while wiping the part clean periodically to reduce additional scratching from particles of plastic and loosened grit from the abrasive.
Once the scratches are removed, I'll transition to Alpha Abrasives 1,000 grit to smooth the surface in preparation for polishing. The next step is a wet buffing with Alpha 40,000 or 60,000 grit sanding films or the grey portion of the Flex-Pad Triple-grit polisher depending on how soft the plastic is. When the clear areas of the part begin to look translucent I'll switch to wet buffing with Micromesh 3200 or 3600 followed by Novus #3 buffed with a polyester swab thence Novus #2 buffed with a microfiber swab. A final buffing with a Kimwipe seals the deal.
The Abrasive Spectrum:
The procedures described above utilize abrasives of decreasing grit in order to remove scratches while causing as little damage to the part as possible. Moreover, there are additional grits in the Alpha Abrasives ranges of both sand paper and sanding films that may be ideal for the plastic with which you're working. I prefer this range of abrasives as opposed to conventional sand papers, which are a bit too rough for use on clear parts. But, they may work for you. In summary it's best to have a broad selection of sanding tools of differing grits so you can match the hardness/softness of the plastic with the appropriate abrasive.
In general, I follow the flow chart below when removing scratches from clear parts. All except the Novus polishes are used with cold soapy water.
Alpha Abrasives 400 → 600 → 1,000 → Sanding Film 30,000 → 40,000 grit Plastic Film or Triple-Polisher
→ Micromesh 3200 → 3600 → 4000 → Novus #3 with Polyester Swab
→ Novus #2 with Microfiber Swab →Kimwipe.
Dipping a Canopy or Clear Part in a Clear Coat:
Once the clear part is buffed to complete transparency I like to protect the finish by dipping it in a clear coat. For many years I used Future floor wax (or Pledge Floor Care with Future Shine as it’s now called) for this purpose. This is available at many grocery and/or hardware stores in the US or can be purchased online.
More recently I've switched to using Mission Models Gloss Coat for protecting all my clear parts after buffing. Mission Gloss covers clear parts more evenly than does Future and is more resilient than Future when dry. I've had dried Future crack on a canopy when removing masking tapes and I've not been able to get dried Mission Gloss to crack under similar circumstances.
For dipping in Future, I use it straight from the bottle. For dipping in Mission Gloss I prepare a 50:50 solution of Mission Gloss in Mission Thinner. Once made I store the diluted Gloss in a sealed bottle for use when needed. Shelf life is not an issue.
Before dipping a canopy in a clear coat I first degrease the part with Windex. Removal of all mold release and/or hand oil is essential to getting an even layer of the clear coat on the part. Future in particular is sensitive to grease and oils and will bead up if the part is not devoid of either contaminant.
After the part is degreased, I submerge it in Future or Mission Gloss and gently buff the entire part with a cotton bud. To do this, I grab the canopy by the framing as best I can with a small pair of tweezers, hold it submerged in Mission Gloss or Future, and buff the entirety of it’s surface with a cotton bud.
I then pull the canopy out of the clear coat and carefully touch it to a piece of Kimwipe allowing the excess to wick into the tissue. The fact that these tissues are lint free is crucial for this step.
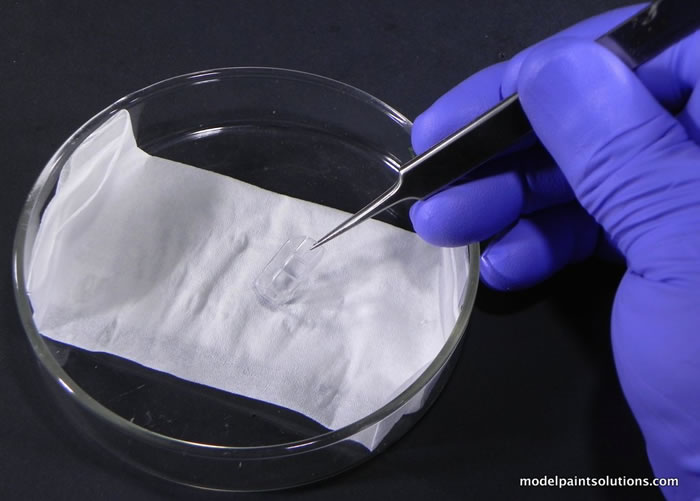
After 20-30 seconds, I dip the canopy back into the Mission Gloss or Future and again remove the excess with a Kimwipe. I due this for a total of 3-4 dips. After the last, I thoroughly wick the excess clear coat from the canopy and carefully place it on a folded Kimwipe in a lidded container to protect it from dust while drying. I’ve used an old glass petri dish for this job for years (pictured). The sealed container is then set aside to dry for a minimum of 24 hours (preferably 48) before it’s handled.
Gluing Clear Parts and Canopies:
I’ve found the combination of dipping a clear part in Mission Gloss or Future combined with attaching said part using only Super-Gold CA Glue (Bob Smith Industries) is a guaranteed way of getting fog- or craze-free canopies.
The gloss coat protects the clear part from the fumes normally given off by normal CA however, Super-Gold CA is described as being “odorless” and it does have less fumes than normal CA glue. When these products (Mission Gloss/Future and Super-Gold) are used together the chances of getting a marred canopy is greatly reduced. Good stuff.
Blending and Buffing Clear Parts After Gluing Them in Place:
As modelers we occasionally encounter a clear part that suffers from bad fit. In this situation we're faced with the task of attaching the part in a way that conceals its marginal fit while maintaining its clear "glass" appearance.
This can be challenging but there are a few tricks that can be helpful. As an example of this situation, I give you the landing light cover from the 1/48 scale Tarangus Bulldog. Although this is a pretty nice kit the landing light suffers from a few fit issues.
Prior to dealing with the landing light cover landing lights were replicated using photo-etch light bulb bases from Eduard (#00-020). Each base received a small drop of "Quick-Cure" Two-Part Epoxy (Bob Smith) to simulate glass lenses. Once these were glued in place and the landing light area painted grey, I set about dealing with the offending light cover.
The cover was first buffed with a little Novus#2 and a Kimwipe followed by a dipping in Future floor wax. After this had dried for two days, it was glued in place with Super-Gold CA. Extra CA was used to fill gaps on each side of the light and to blend ridges at the top and bottom where the light was too large for the allotted space. Note the lack of crazing/fogging of the clear part due to the use of a cleat coat (Future) and Super-Gold CA (Bob Smith Industries).
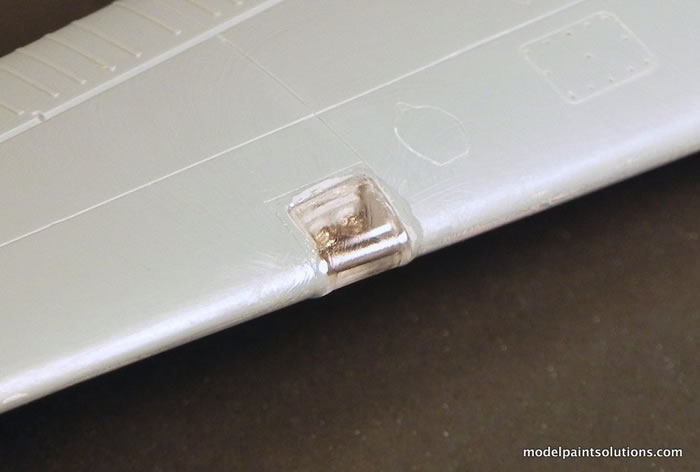
The landing light cover was blended by wet sanding with Alpha Abrasives 400, 600, and 1,000 grit papers used with cold water containing a few drops of dish soap. A final sanding was performed with a sheet of 1,000 grit sanding film.
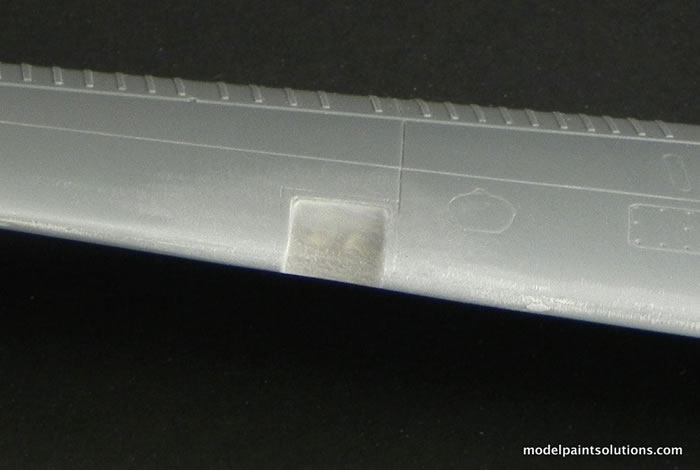
With the correct shape achieved and blended, I set about polishing the plastic back to clarity. After some trial and error I found that for this particular plastic, an initial buffing with the grey portion of a Triple Polisher stick worked well. This was followed by buffing with a sheet of 40,000 plastic sanding film thence a rigorous buffing with a 3200 grit Micro Mesh Pad. All were used with cold soapy water.
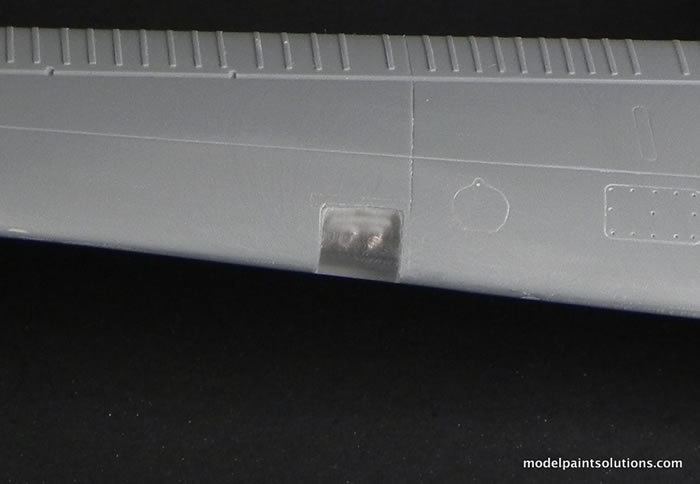
Further buffing was performed with sequentially; Micro Mesh 3600, 4000, and 6000 pads. At this point, I opted to skip Novus#3 and buffed the cover with Novus#2 and a Micro Mesh swab. Knowing when steps and/or grits can be skipped is more a matter of 1 part experience, 1 part guessing, and 1 part trial and error. With more experience it becomes easier to determine the combination of abrasives best suited to the clear plastic with which you're working.
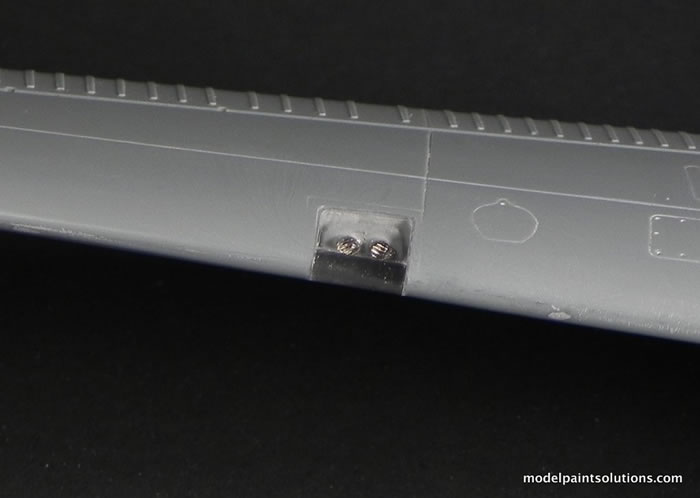
To finish up, the cover was buffed with Novus#2 and a Kimwipe followed by a vigorous buffing with a final, dry Kimwipe.
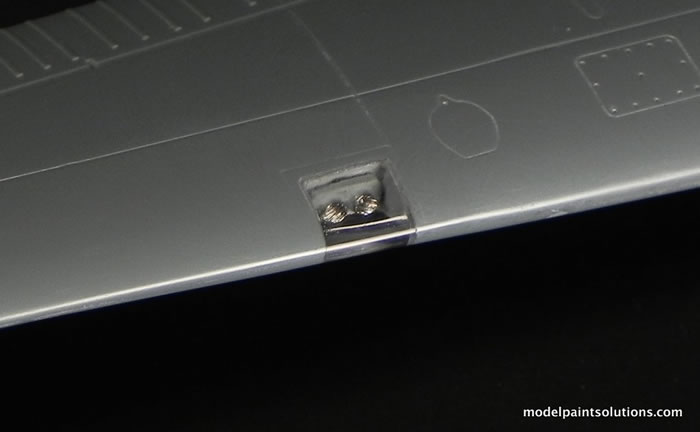
Done!
I hope you found something helpful there. Like many of the techniques we use in scale modeling, polishing clear parts to complete clarity requires good working light, patience, and practice. Considering the clear part of a model, be it a windshield or canopy, is a focal point of most builds makes taking some extra time to get these parts crystal clear well worth it.
For more information on this article visit ModelPaintsolutions.com
Model and Text Copyright ©
2017 by Model Paint Solutions Inc.
Page Created 15 December, 2017
Last Updated
16 December, 2017
Back to
HyperScale Main Page

|